The mechanical team has been hard at work this semester, making strides on both our main bot and minibot projects! Here’s a quick update on what we’ve been up to.
Oogway Updates
Materials Ordered for Self-Propelled Torpedoes
We’re excited to announce that we’ve ordered all the materials needed to prototype our first self-propelled torpedoes. After testing passive torpedo designs last semester, we found they lacked precision and reliability. Our new design uses a supercapacitor, a small DC motor, and a propeller, which we hope will give the torpedoes a more controlled trajectory. With these new parts, we’re looking forward to starting assembly and initial testing soon!
Thruster Mount Upgrades with SLS Parts
One of our priorities this semester has been improving the durability and aesthetics of our main bot. We’ve replaced the thruster mounts with new parts printed from Nylon-12 using an SLS printer. These mounts are significantly more shock-resistant and watertight, which is essential for keeping our bot reliable in competition. The new material also gives a cleaner, more professional look to the underwater components. We have begun to replace outward facing sensor mounts as well. The final step will be color coding externally visible internal mounts to match the color scheme.
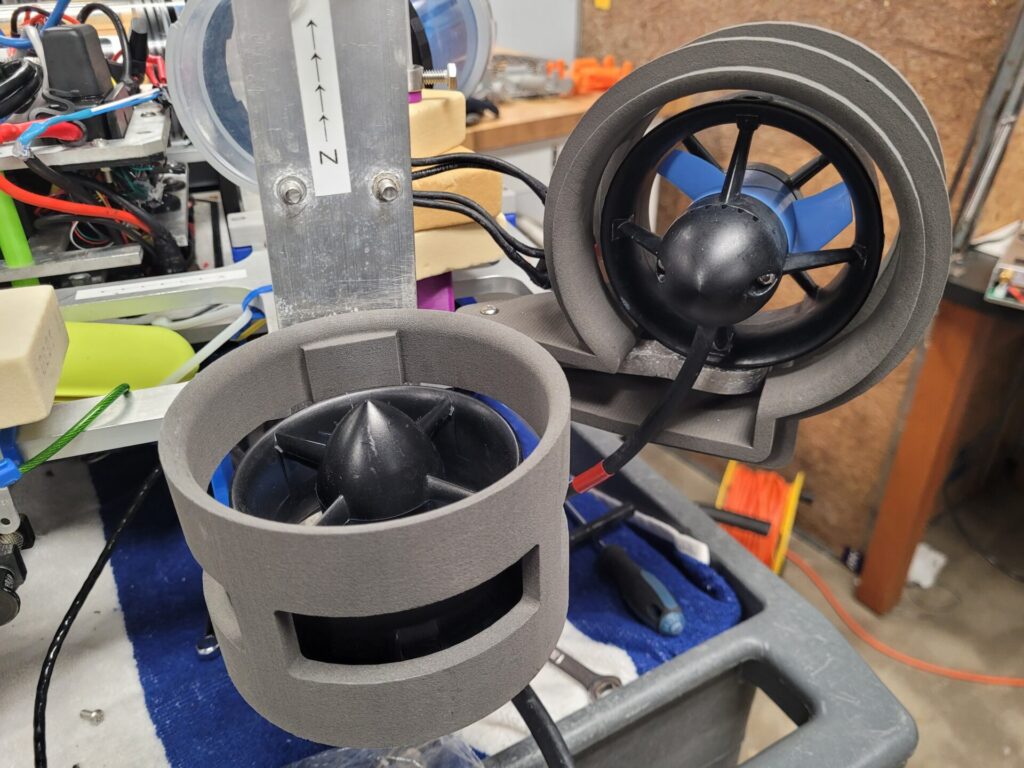
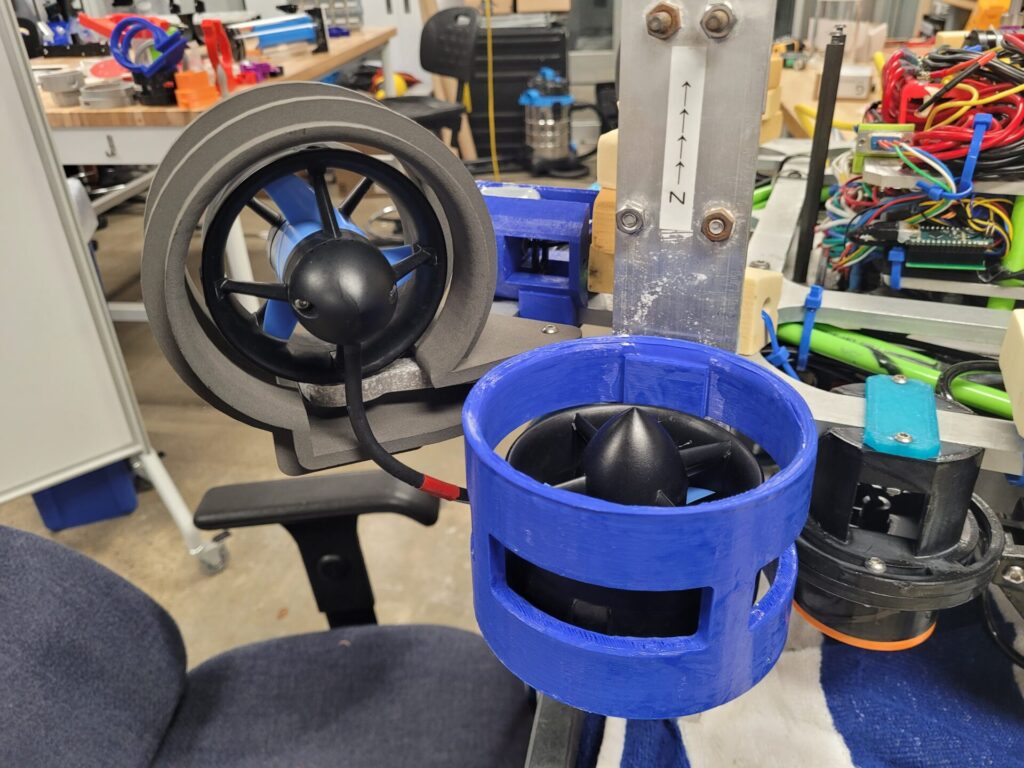
Redesigned Marker Dropper
Last but not least, we’ve been reworking the marker dropper mechanism to make it more reliable and easier to reset. The new design features improved release mechanics that will reduce accidental drops and keep the deployment consistent during testing and competitions. We’re confident this redesign will give us better control and efficiency in the field.
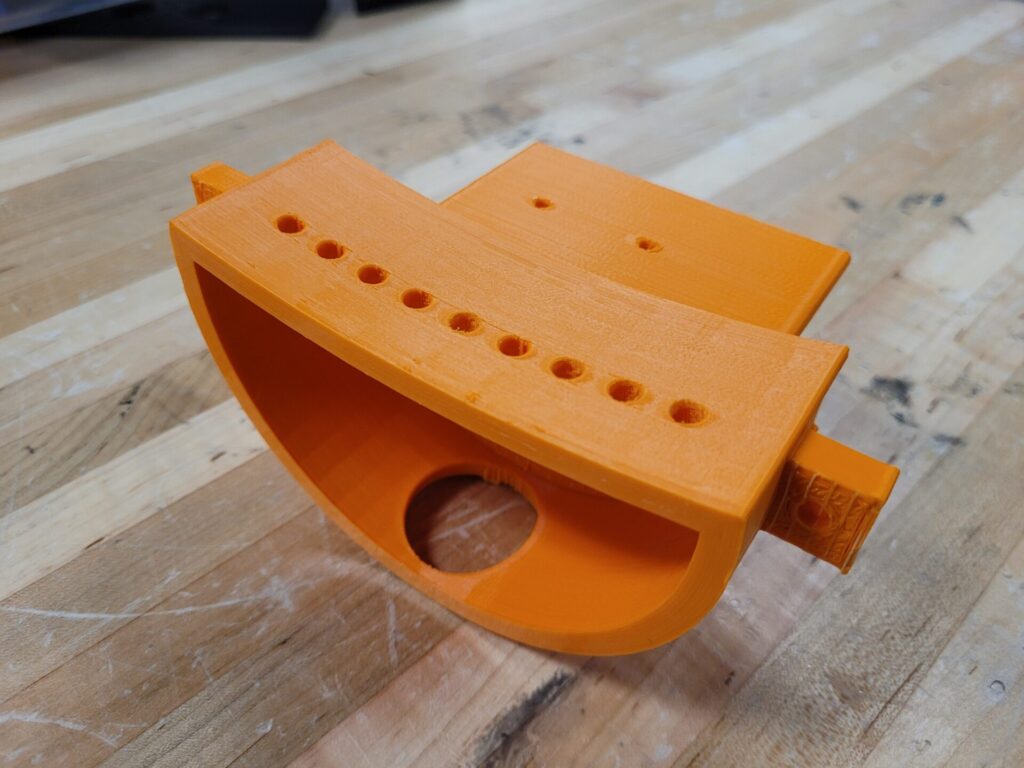
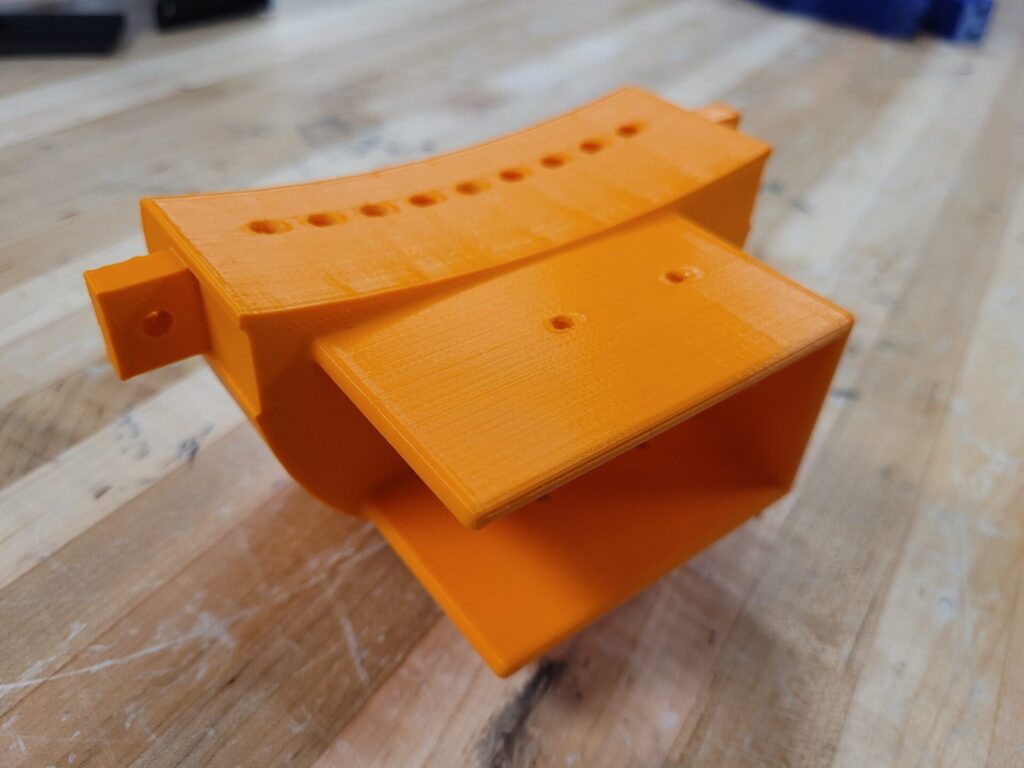
Redesigned Buoyancy Mounts
The old buoyancy mounts had a thin rod of PLA plastic, making it prone to breaking under stress. The new design incorporates hollow aluminum tubes so that we get much stronger rigidity, shorter print times, and maintain the lightweight nature of the mechanism. We also incorporated brass inserts into the mounting bracket and rod-securing mechanism to streamline installation and removal.
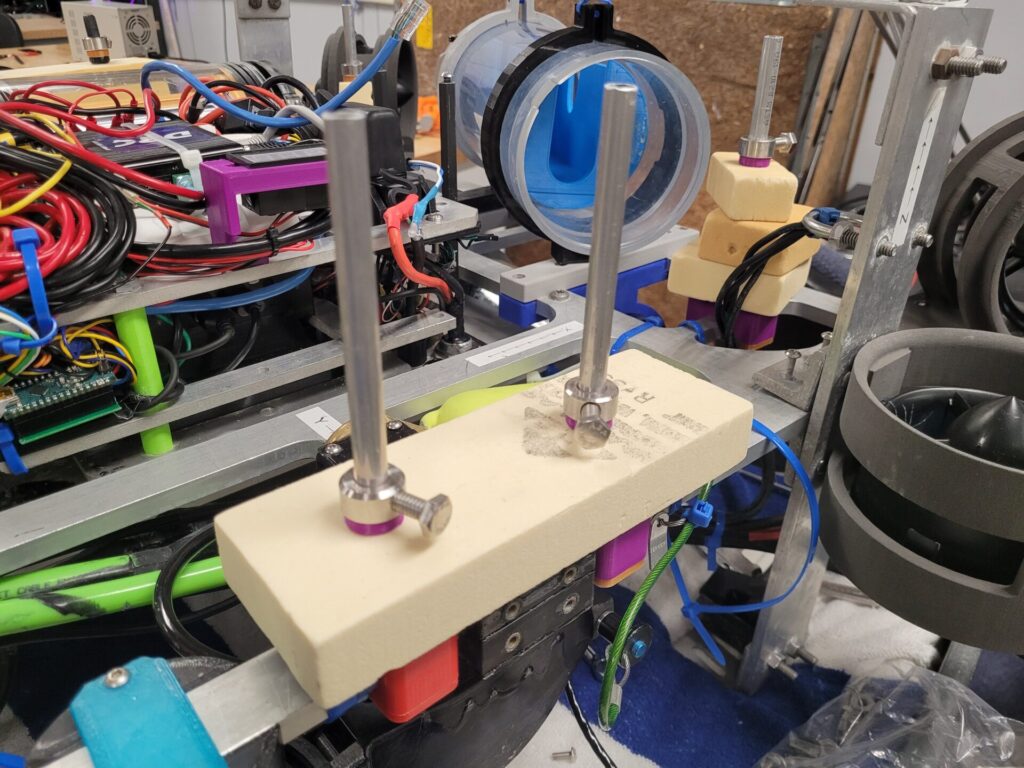
Minibot Updates
Simulation
Our minibot design has gone through several iterations as we fine-tune it for optimal performance. To get to our current concept, we’ve run multiple fluid simulations to assess water flow and resistance around the frame. These simulations have been invaluable in ensuring the frame allows for smooth movement and stable control underwater.
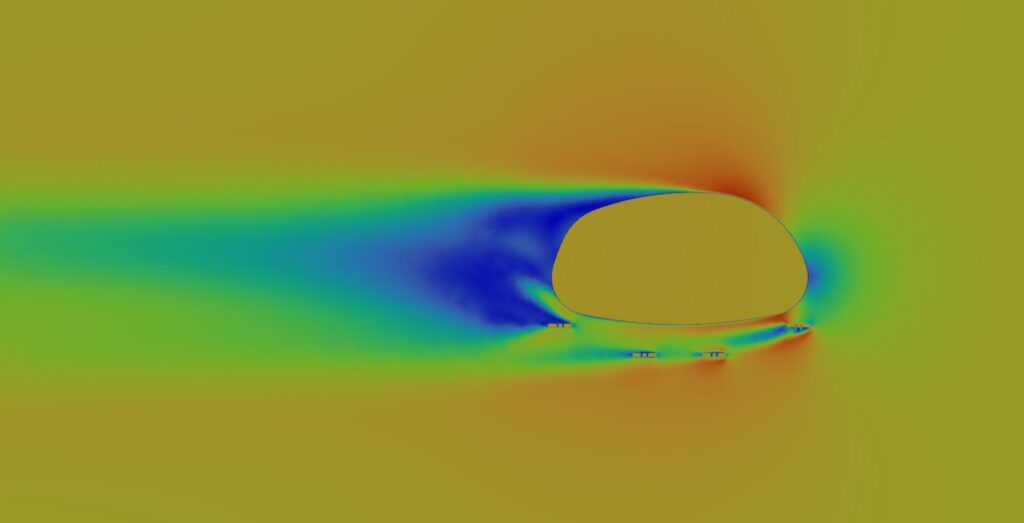
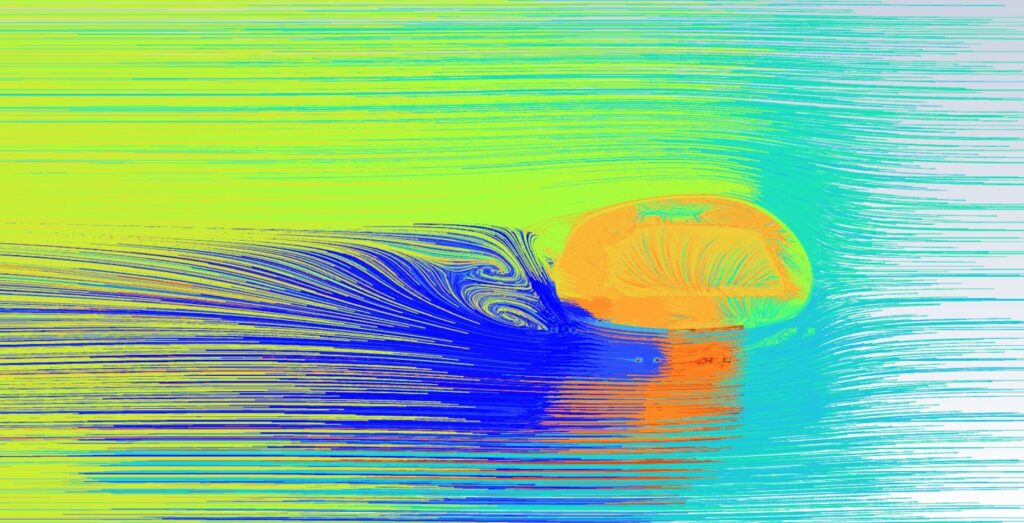
Model Design
The frame will support six thrusters, enabling versatile movement while keeping the minibot compact. We’ve also included mounting rails with a uniform pattern, which will allow us to add components, like cameras or sensors, in a modular fashion.
Meanwhile, our internal capsule design team has made significant progress in arranging the components inside. They’ve focused on placing heat-producing elements near large metal standoffs that extend to the end caps. These standoffs act as heat sinks, helping to dissipate warmth and keep the capsule cool during operation. This setup should help keep capsule conditions stable during long pool sessions and during high intensive maneuvers like the barrel roll.
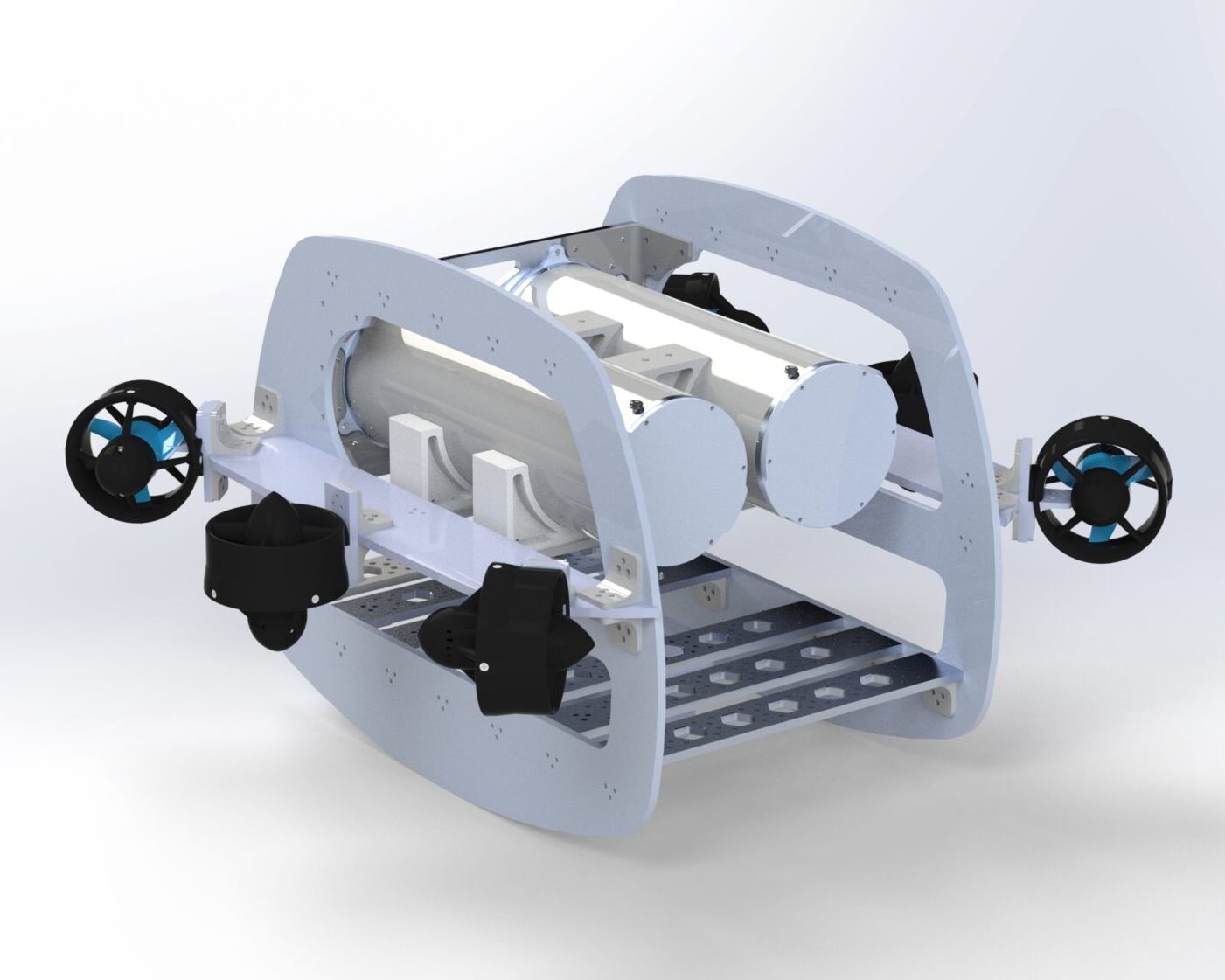
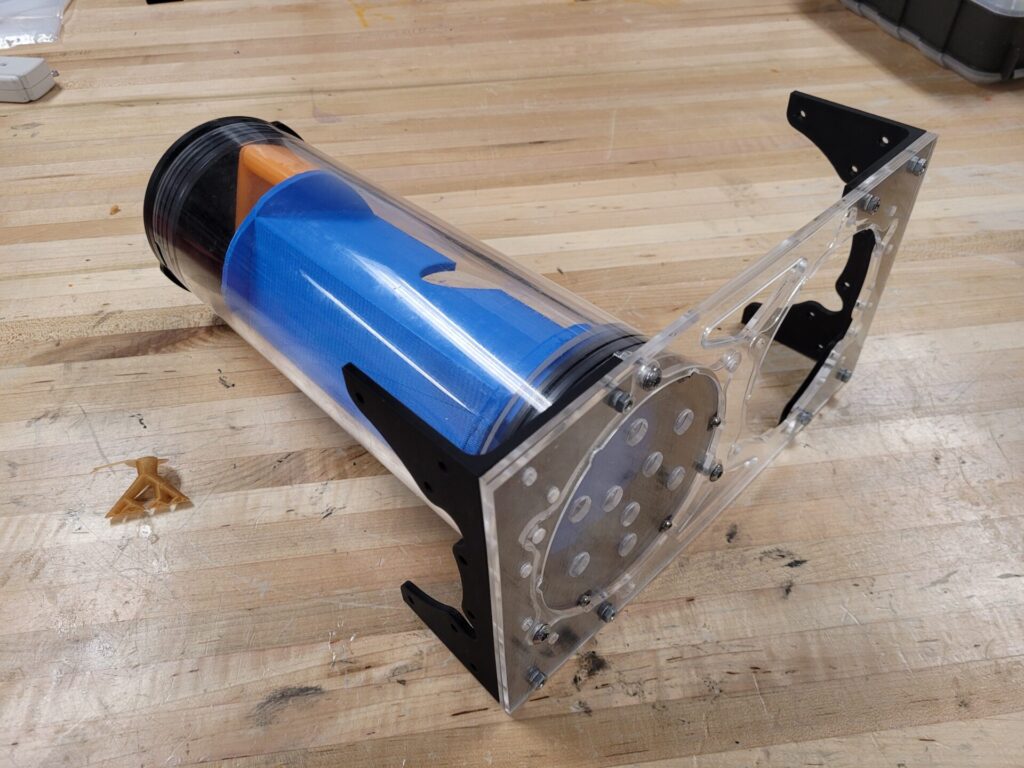