Minibot
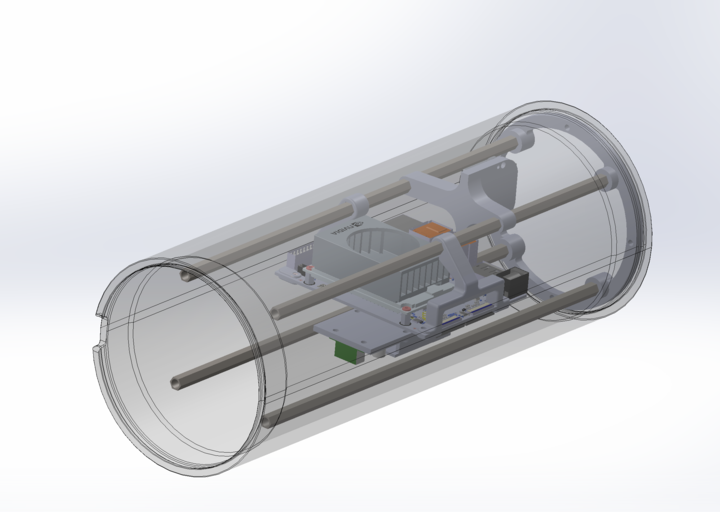
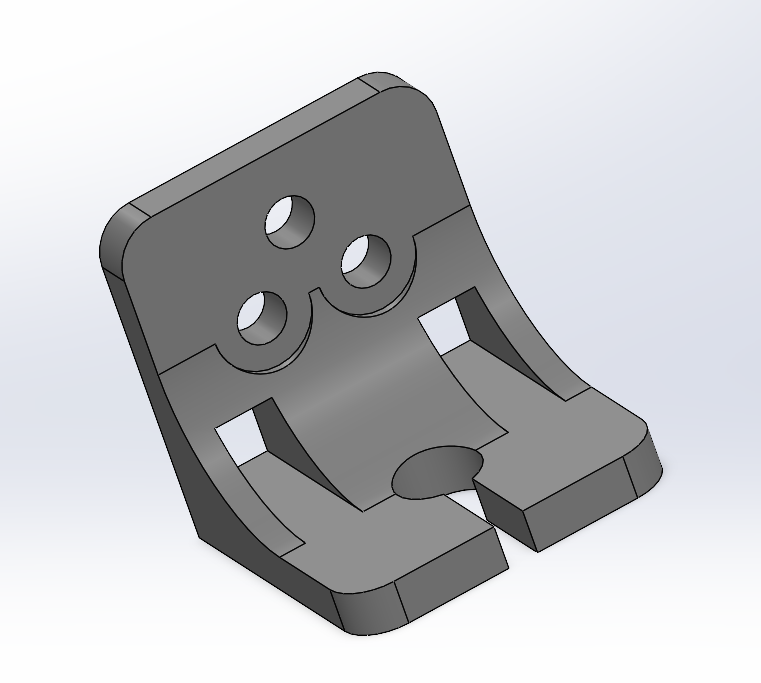
Ethan and Lily have been working on mounts for the mini bot electrical stack. They’re making steady progress in incorporating all our new components, such as the Jetson Nano.
Danny is focused on building the camera housing, ensuring it is robust and functional for the team’s needs. His work is a crucial part of the overall design and helps ensure the camera is well-protected during operations.
Meanwhile, Nico has just completed the final review of the case, providing the team with confidence that the design meets all requirements.
Michelle is working on the hydrophone mounts for the minibot. These are being adapted from the current design from Oogway, but need several changes to mesh with the new standard mounting pattern on the minibot.
Torpedoes
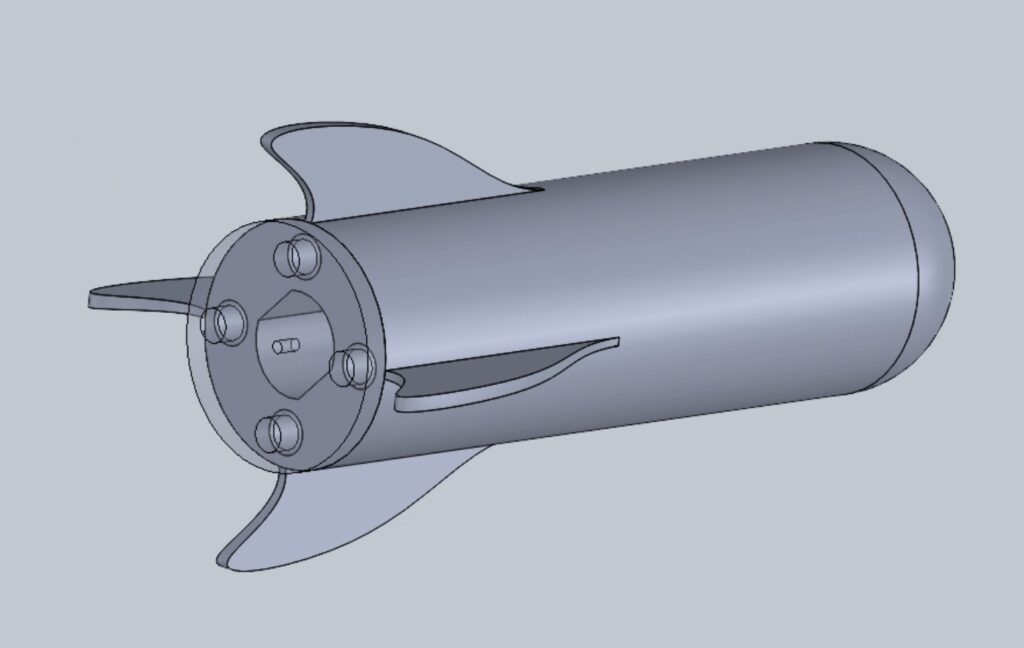
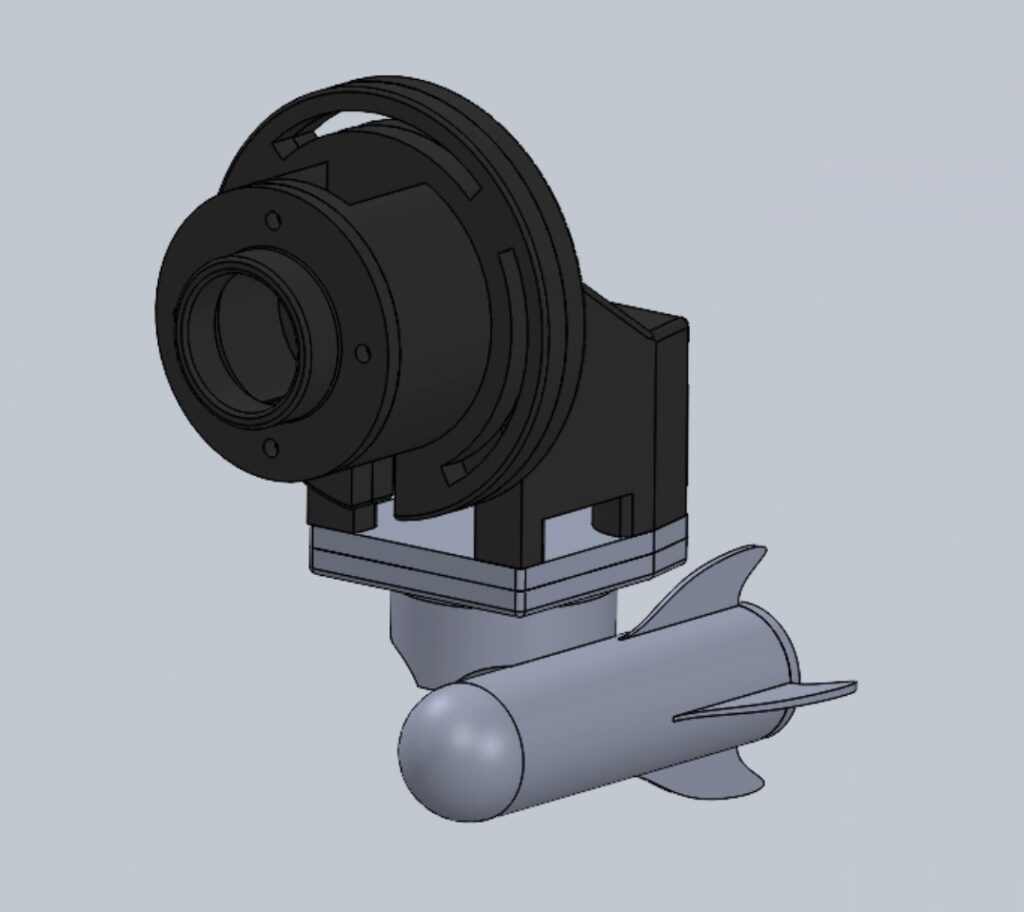
As the semester wraps up, we finally got the order for our micromotor in. We also have a preliminary design for the actual torpedo and attachment method. Our current plan is to use an electromagnet to hold the torpedo in using some magnets embedded in the torpedo. Inside the torpedo, we will have a normally-closed reed switch in series with a supercapacitor and our micromotor. When the electromagnet turns off, the reed switch will close and the capacitor will power the micromotor, sending the torpedo off to its target!
We are still working through some issues with the circuit, such as how to independently fire two torpedoes, but we’re aiming to get a proof-of-concept in Janurary.
We also have a second, more traditional torpedo prototype in the work based on a spring and release servo mechanism. Raine, Chloe, and Michelle are collaborating on the torpedoes, working diligently to perfect the design and functionality.
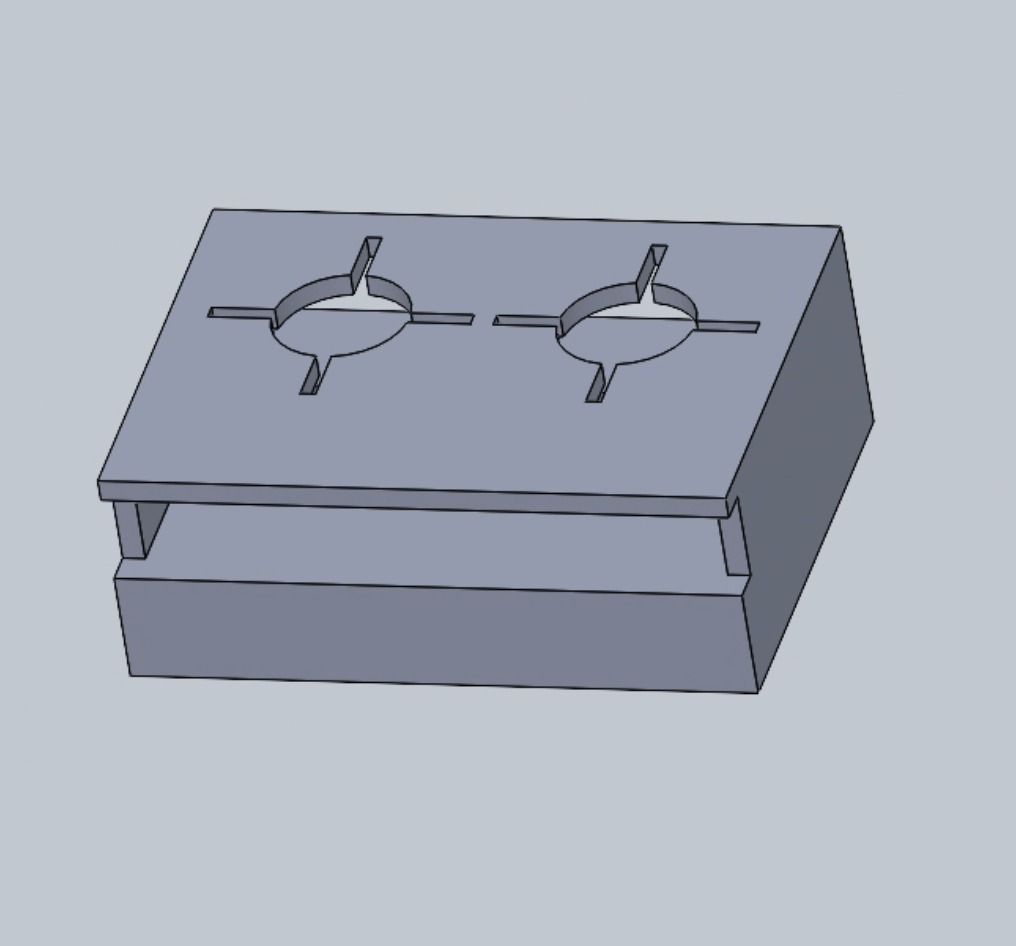
Other Mainbot Changes
Due to the weight of our new 100% infill SLS 3D prints, we realized our buoyancy blocks were insufficient! We filled the entire adaptable buoyancy system and the robot was still negatively buoyant. Therefore, we cut new buoyancy sheets, which are about 3-4x the size of our standard size to mount on the robot.
We have also finalized the design for our new battery capsule holder. The earlier design required that the capsule slide out from the side, which was difficult and caused it to break under repeated stress. Our new design, developed by Ivan, opens up and secures with a hinge on the top, which allows the battery capsule to be much more easily removed and replaced. The 3D print itself is also a lot thicker, which makes it more resistant to stress. We will be doing some real-world testing over the next few pool tests to ensure the design holds up.
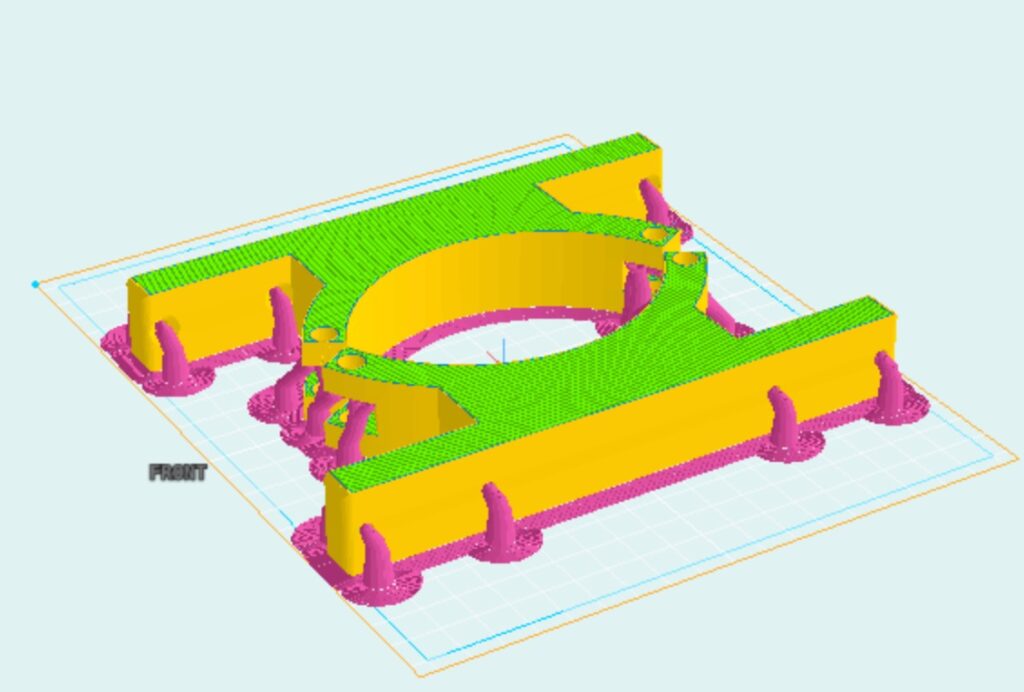
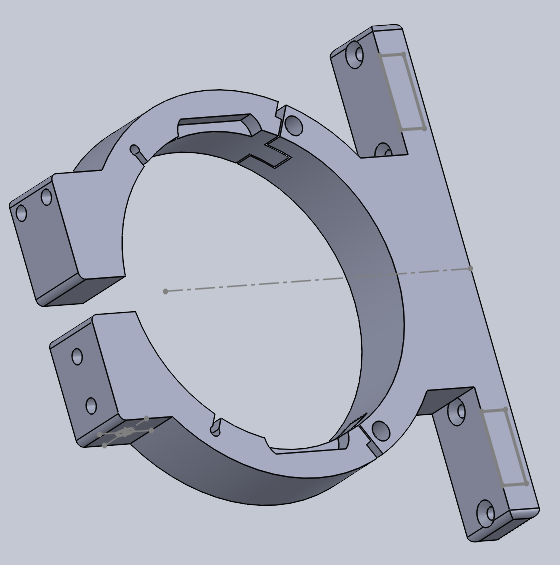
Ari is focused on remaking hydrophone mounts for the big robot. The old mount required that the hydrophones be zip-tied in, which made their mounting angle inconsistent. The new design will fix this issue and make the entire system more stable and robust.