Now that the mechanical subteam has completed the internal structure of our minibot, Crush, the electrical team has been hard at work hooking up all the wiring. Our veterans, Joyce and Carson, worked on prepping and routing the intercapsule Ethernet cable. Since working with Ethernet cable is always challenging, we bought screw terminal blocks that will allow us to avoid soldering directly.
Our new members, Monish, Jill, and Rachel, soldered the relays and battery connectors necessary to turn the robot on. Soldering to the flat relay heads proved a bit challenging at first, but they eventually got the hang of it.
While half the team was away pool testing, Patrick and Maanav had a long wiring session where they made significant progress on the power and signal capsules. The main power infrastructure is complete. All that is left is adding a temperature and humidity sensor and connecting the relays to the on-off switches. Since this is a permanent connection, we are saving it for last in case any more changes are needed. To make this connection more modular, we are looking into using the screw terminals. However, they may be too large for the capsule.
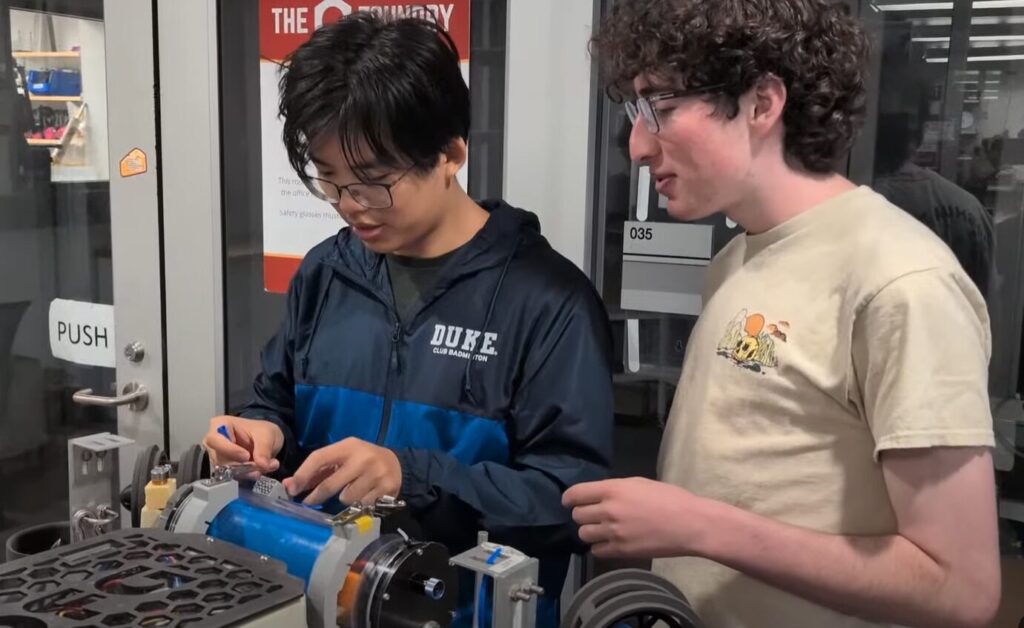
One of the major challenges we’ve had with wiring is not having enough space for the wires themselves. Several parts had to be redesigned to account for the thickness/length of cables, and overall, there is not much extra space in the capsules. The mechanical team has noticed this and will consider wiring in future designs.
Despite our minibot getting most of our attention, we haven’t forgotten about Oogway. Every week has brought new challenges, fixes, and updates on our big bot. Most recently, we hooked up a new fiber-optic gyroscope. Last year, yaw-drift was a big problem as it caused Oogway’s “north” direction to shift over time. We traced this issue back to our IMU, which drifts over time. This fiber-optic gyroscope has extremely low, essentially negligible, drift over time and should solve our yaw-drift problems.
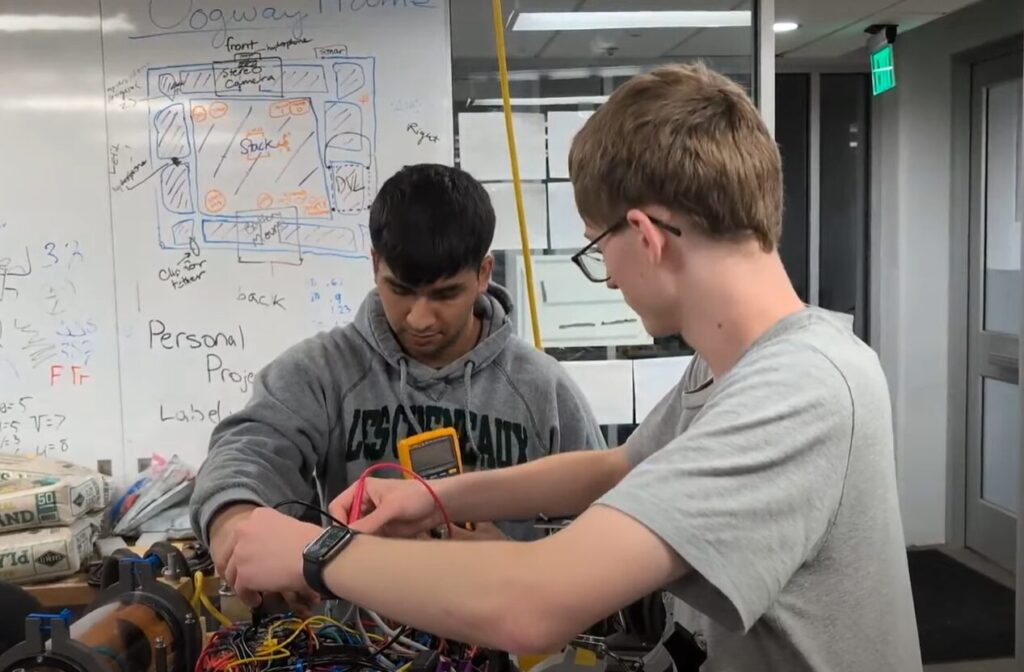
Wiring and data extraction proved to be a challenge with this sensor. We had to solder the power connections on the robot itself, and no matter how steady the hand, sticking a hot soldering iron into the center of the stack is always nerve-racking (challenges like these are what inspired the modular and accessible design of the minibot). Additionally, the gyroscope requires a 1 kHz trigger signal to transmit angular data. Since the computer can’t effectively generate this signal, we used an Arduino and hooked it up between the computer and the sensor. After debugging the Arduino clock for a bit, we were able to extract gyro data!