The mechanical team is excited to hit the ground running this year with a fun onboarding project and plenty of tasks for returning and new members. This semester, we tasked new members with building a paper bridge that could hold as much weight as possible. We had so many interesting and creative designs!
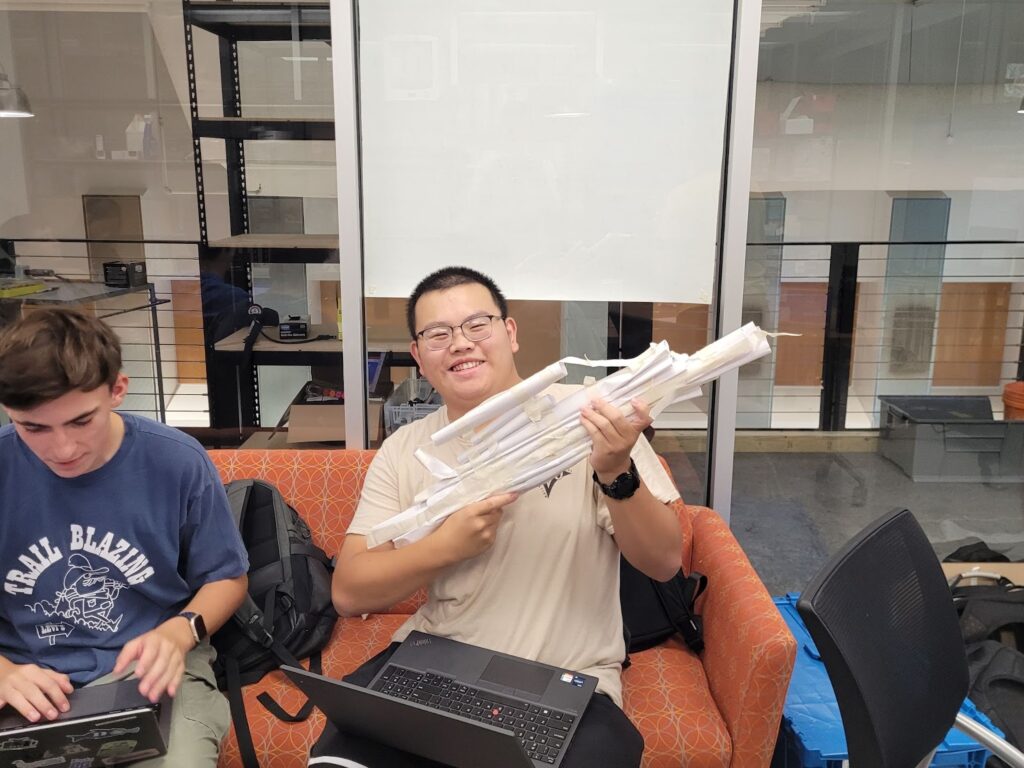
For the next part of onboarding, our new members got used to using SolidWorks by redesigning Oogway’s buoyancy mount, which had broken often during competition. They learned to create sketches, extrude, cut, fillet, and so much more! The new members also got familiar with using tools like calipers and 3D printing their new designs.
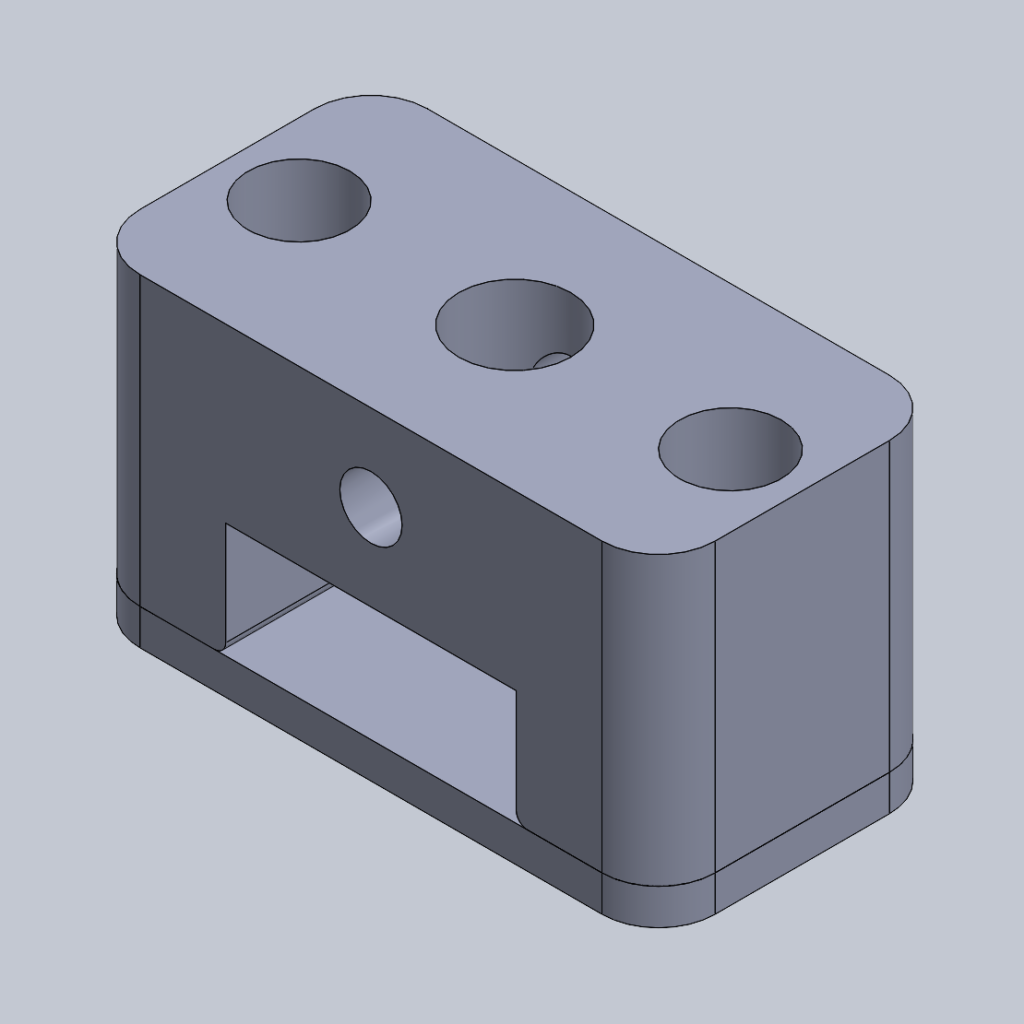
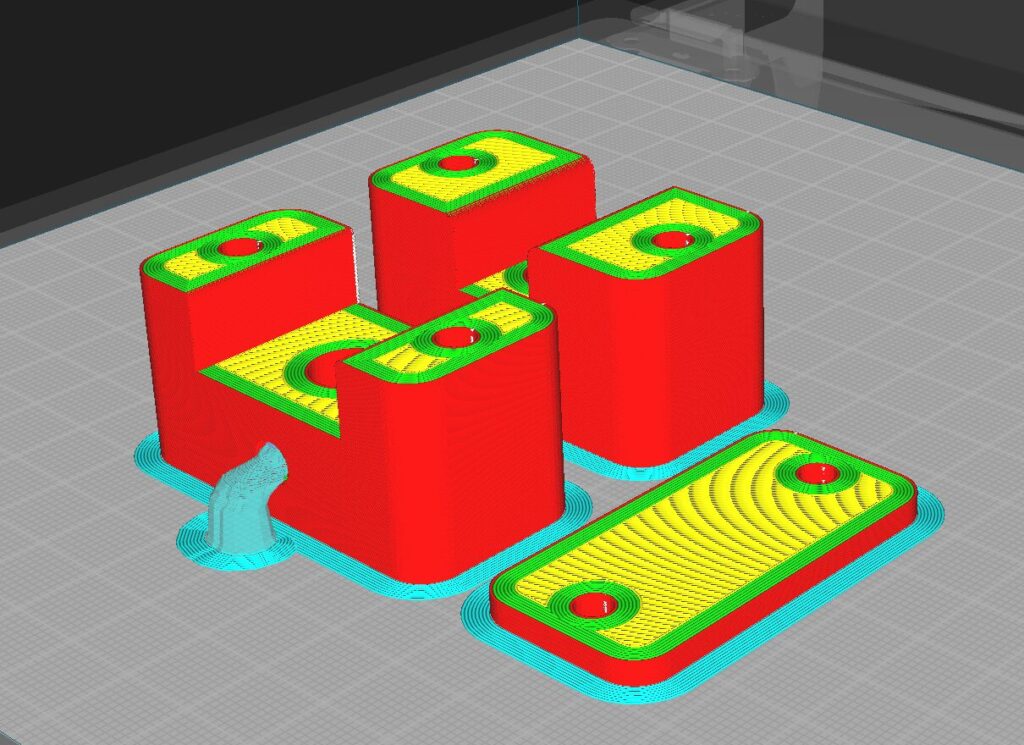
We also took all our new members on a tour of Duke’s premier design space, the CoLab, where they learned how to use the waterjet cutter. This will be a tool we will be leveraging often this year as we mill the frame for our new minibot.
On the topic of the minibot, we’ve been making steady progress in finalizing the design and components list. It features two side-by-side capsules, one which contains most of the electronics, and one which contains the battery. We plan to have six thrusters to allow the sub to move freely in most directions, while still keeping it compact. The frame below contains several mounting rails to allow us to add additional components in the future, like a camera or a claw. The next steps for us are to get an initial full CAD of the sub and then start building!
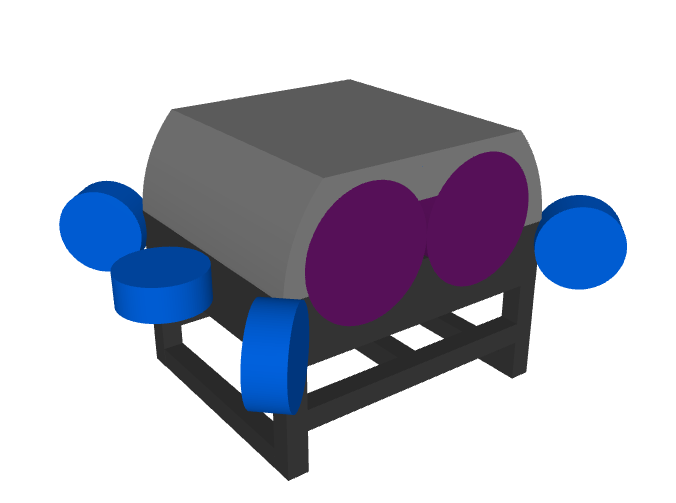
On the main bot, we have just a few tasks we’re finishing up from last year. We received some feedback from judges regarding the disparate coloring of our 3D prints, which, although it looks cool, is not very professional. As such, we’ve decided to reprint all of our water-facing mounts on Oogway with Nylon-12 using an SLS printer, which will make everything from our thruster guards to sonar mounts more shock-resistant and watertight.
Besides the buoyancy mount, we’re also in the process of a slight redesign of the stereo camera mount. While we have not experienced too many problems with the current design, it does have the possibility of rotating inside the camera capsule over time, leading to an unreliable FOV. As such, we added a gear-like design to the outer circles so they can lock into the notches in the capsule.

Finally, the next big step for us is to implement a torpedo launcher on Oogway. Testing from last semester showed that a passive torpedo (i.e., one that is launched by a spring) tends to veer off course and is difficult to reset due to the high spring constant needed.
This semester, we’ll be trying an active torpedo which contains a supercapacitor, a DC motor, and a small propeller. We hope that it will simplify the launching mechanism and provide a more reliable shot.