We had our first pool test of the year! New members got to see the robot in the water for the first time (they even got to see some barrel rolls). Of course, this pool test was not without some drama. The power cable from the battery capsule to the main stack, through a combination of corrosion and wear and tear, had a nearly broken lead, which was stopping the relays from turning on. A quick solder and epoxy job served as a temporary fix for the pool test, but making a new battery cable is a top priority for the electrical team!
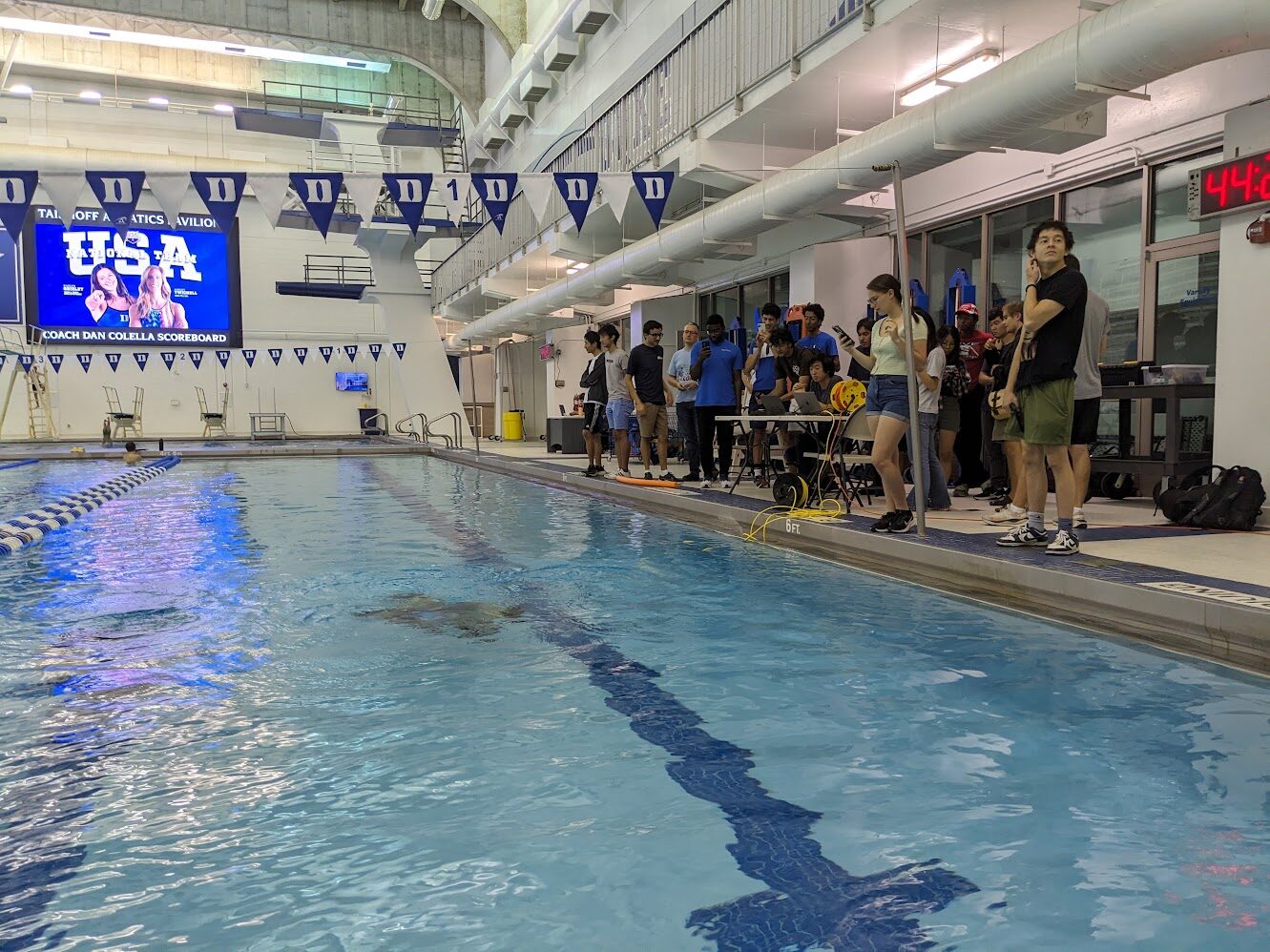
Over the past few weeks, new members have gained a much clearer understanding of their projects and begun progressing. Our team working on building out Oogway’s electrical stack on a piece of wood has completed the portion that powers the high and low power circuits. It took a bit longer than expected since this was the first time many of them had done this kind of soldering. Soldering to relays and buck converters was particularly challenging. We also ended up removing our kill switch design. Instead of having a master kill switch for the whole robot, we will stick with our two-switch system and make the thruster switch more obvious and easy to press. The point of the kill switch was to make it easier for the diver to stop the robot and bring it back to start another run, but turning off the whole robot would mess with how CS has set up controls and task planning. We can achieve the same goal by making the thruster switch more prominent and easier to press. Now that all the changes have been implemented, the wooden stack team is going to test what they have soldered and hook up the computer.
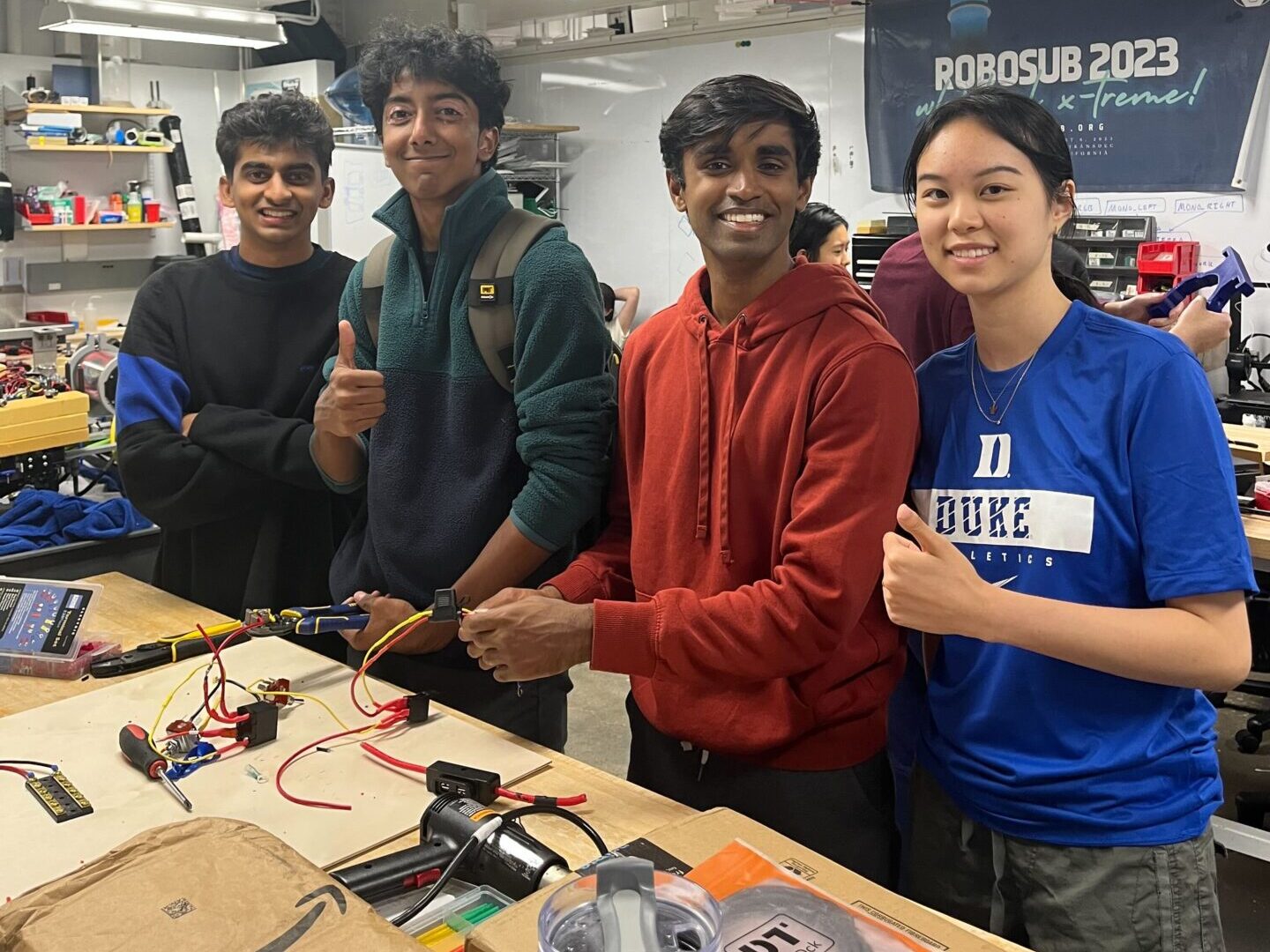
While Oogway’s wooden stack is making progress, the minisub stack is essentially complete! The ESCs need to be soldered with longer cables, but during our last meeting, they were able to power up the Raspberry Pi (serving as a temporary computer for the minisub) and ssh into it. Since we will be making custom PCBs to replace the Arduinos for ESCs, Lilly led an intro to PCV design using KiCAD. A good chunk of our new electrical members now know the basics of PCB design, and we have a dedicated team moving forward with designing the PCBs needed to replace the thruster Arduino with ESP32s.
Finally, we have begun working with the mechanical team to integrate the electrical and mechanical components of the minibot. Mechanical has gotten dimension and weight measurements of our current minibot stack to determine the size and placement of the minibot capsules.
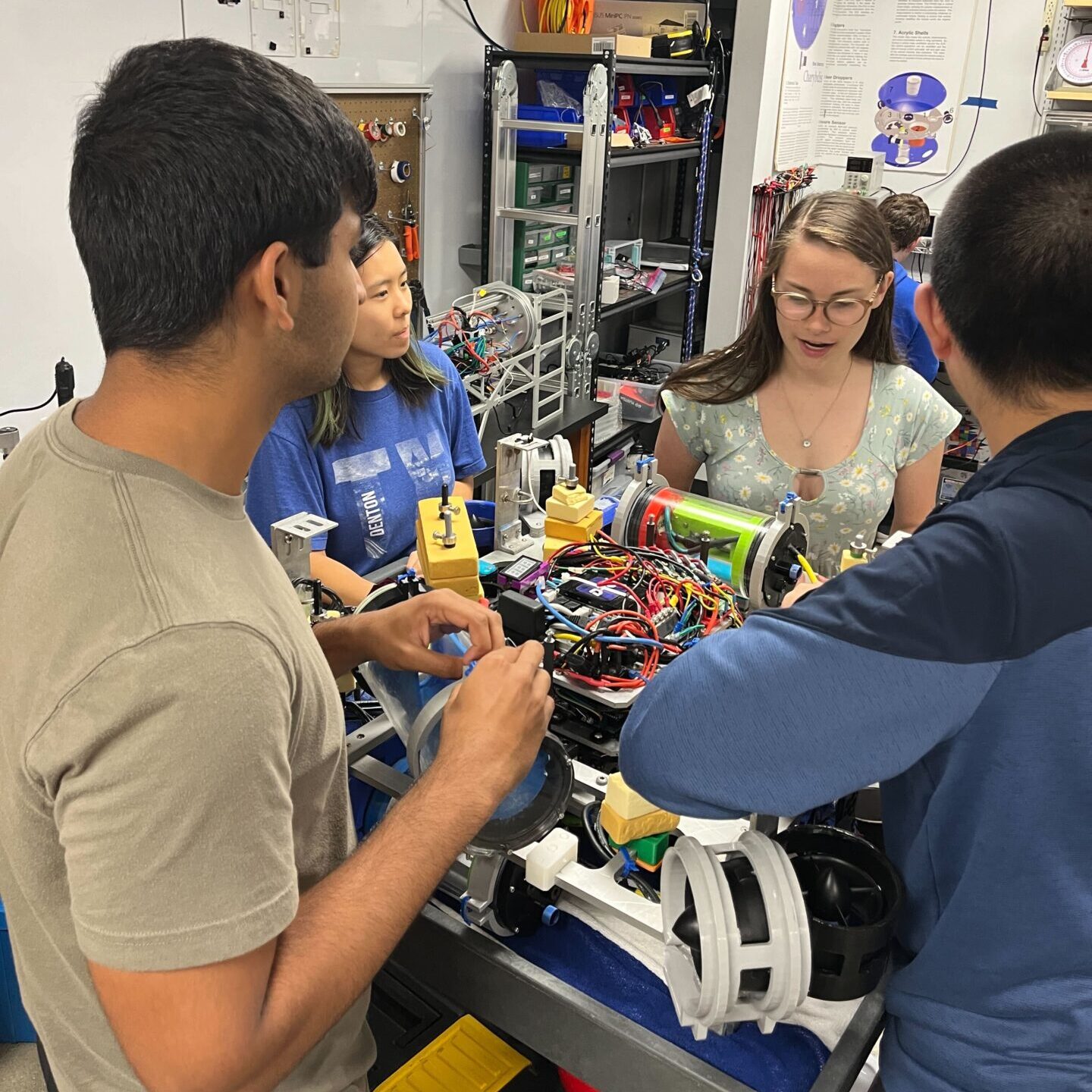